Get The Support You Need!
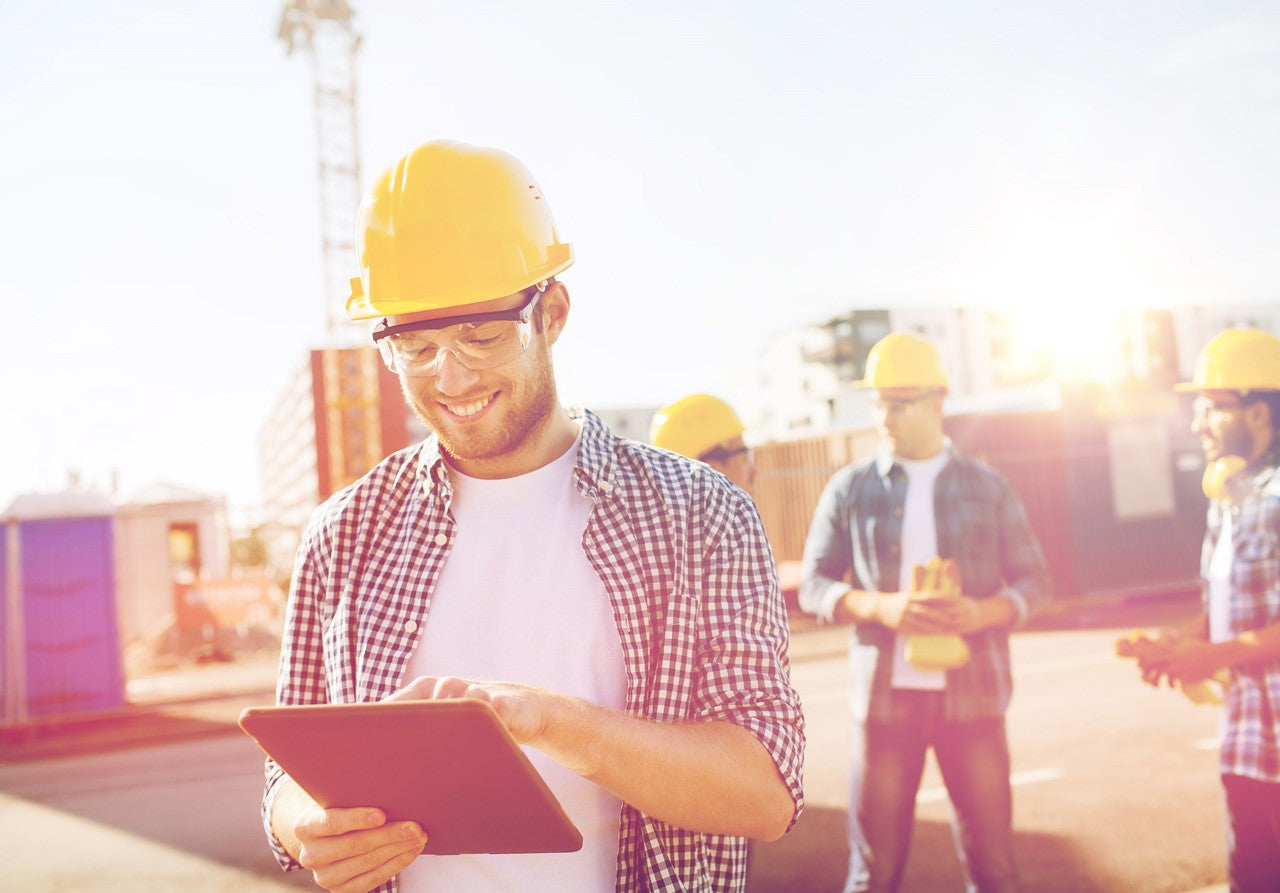
Safety Procedures Help Your People and Your Profit
Safe operating procedures can help your people and your profit, but this won’t happen without deliberate decisions and strategic action. To see people and profits improve, we must think about safety procedures in a helpful way, support people with constructive work-culture, and equip them with easy to use resources. In this article, we’re going to consider all three actions.
This can be a self-serving process. When we help you, you are better able to help your people, and your people help your bottom line. Perhaps the idea that safe work procedures can improve your bottom line (rather than drain it) seems comical, but I invite you to journey with the idea.
Thinking About Safety Procedures in a Helpful Way
Anyone can issue safe work procedures, but implementing them effectively, consistently and profitably requires a mental ‘wrestle’. Contending with these thoughts might feel threatening, and many are not willing to step into that ring. But it is necessary!
A Complexity Worth Recognising
The question is one of ‘perspective’, not ‘attitude’. ‘Perspective’ stirs awareness of distance, angles, preconceptions, differing viewpoints, varied agendas and multi-dimensional considerations. Work health and safety has that level of complexity. To call this a simple matter of ‘attitude’ seems too fixed, too emotive, too hierarchical and potentially very, very negative.
We are wise to acknowledge this complexity.
When our Thinking is Clear and Resolute
When we adopt a helpful perspective toward safe work procedures, we adopt clear objectives with absolute resolve. A commitment that lasts despite opposition is required. Inconvenience or expense should never be prioritised above the health and safety of your people.
Absolute engagement is great, but let's accept that this challenge is significant:
- The Work Health and Safety industry has its share of shonks and charlatans.
- Many WHS investments are genuinely big-ticket items, and
- There are a multitude of documents, decisions, processes and ever-changing regulations to keep abreast of.
Even when investing wisely and dealing with ethical suppliers, safe work procedures always have a price. Waning commitment, when confronted by annoyance or expense, is not helpful. Many want safety, but without the pain (and that is, indeed, ironic).
It is actions, not mere words that help WHS outcomes. As employers, managers and leaders, we rate workers by what they do, not what they say. Our staff, contractors, site visitors and more do the same thing. They watch how leadership implements and values safety systems, plans and procedures. They judge us by our actions.
We are in a helpful space when we adopt and enforce safe work procedures, not because of fines, but because of the value placed in Jose, Sue, Vladimer, Marty or (you fill in the blank). Your sincerity and sense of responsibility matters. Consider a parallel situation: most adults improve their driving when they've got children on board; not because it's the law - but because they passionately care for and value their precious passengers, and these passengers know it.
Therefore, when implementing your safety procedures:
- Give serious thought to what others see when they look at you and your leadership?
- Factor in the perspectives of the many people involved.
- Test your commitment.
I sincerely believe the question of care is ground-zero when there is an accident or incident: if it happens, then someone, somewhere, did not care enough!
Supporting Via Work-Culture and Safety Procedures
Once you've got yourself in a healthy and productive space, you can effectively focus on others. You have a multitude of different people to accommodate, support and lead. Doing this will be easier if you have developed a safe work culture. But how do you do that?
Here are four suggestions:
- Be aware of the many people you need to accommodate,
- Model the behaviour you want,
- Discourage corner-cutting, and
- Ensure every person has the right to say “No” and “Whoa”.
Safety, Procedures and the Many People Involved
The task is easier when you only have your staff to worry about, but that is rarely the case in our industry. Usually, you also need to guide, police and empower:
- Staff,
- Contractors,
- Subcontractors,
- Visitors and
- Clients
All of these groups think differently. Likewise, no one individual in any of these groups will think precisely like the other. As a result, collectively, they present quite a challenge.
To help with the subby factor, and as a promotion for this article, we’ve created the Subcontractor Management Pack. It brings together four separate resources for just $50 (down from $81 at a 37% discount). You can see this discounted resource here.
Your Staff Lead Your Safe Work Culture
All the groups just mentioned contribute to your workplace culture, but it is your staff and leadership that plays the most significant role. Your safety procedures will pencil an outline, but it is what your team does and says that puts the substance, significance and colour between those lines. Every safe work procedure enforced, and every behaviour modelled, makes a profound difference.
The results are in: behaviour modelling has shown that what leaders do matters most. People are more likely to perform behaviours that are consistently modelled by others.
The leadership of your team will shape your culture.
Safe Work Procedures Do Not Cut Corners
Every safe work procedure forms part of a greater whole. Every procedure matters! Build this perspective into your work culture, and quality outcomes across the board will be the natural by-product. Eventually, your bottom line must also benefit.
Do you remember the 2005 Sea King helicopter crash? Nine Australian Defence Force personnel died, and two others were severely injured. Wives, partners and children lost their husbands, partners and fathers. Why? Because of a failure involving a part that cost less than $1 and a process that required seconds. What happened? A nut and split pin had been incorrectly refitted during maintenance - and ten individuals were found to be culpable in that error.
That ‘relatively tiny’ error was indicative of a much larger problem. The inquiry that followed identified an “embedded culture of shortcuts and workarounds” and “a complex interaction of individual and systemic failings”. There were 256 recommendations by accident investigators, which resulted in an enormous overhaul of safety procedures.
Here’s the point: we need to view every safe work procedure as an absolute necessity. It could save a life!
Safe Operating Procedures Give Everyone the Right to say “No” and “Whoa”
Your safety procedures are helping people when every worker, and even every site visitor, is empowered with the right to say "No" and "Whoa", wherever safety is concerned. Override decisions by authorities are appropriate once a concern is assessed, but always ensure there is a fundamental freedom to voice a concern.
As I thought about an “embedded culture” of corner-cutting in the Royal Australian Navy’s Aviation Group, I got to thinking. Surely, there must have been times when a Seaman, Leading Seaman or maybe even a Petty Officer saw the problems that led to this fatal maintenance screw up:
- Was it the rank structure that got in the way?
- Was there a complexity or a cultural casualness that destroyed clear, honest and life-saving communication?
- Did personal career interests create hesitation in those who wanted to voice their concern?
Surely, someone must have recognised that safety procedures weren't adequate. Perhaps one of the ten people found culpable had previously realised the problem. Perhaps, they figured it was someone else’s job to speak up. Maybe they did speak, but no-one was listening. What a tragedy!
How do your safety procedures compare?
Can people speak out their safety concerns? Can the Seaman in your team say "No" to the Captain - even the Admiral? Will they get demoted or sent to the brig for speaking up? Does your Petty Officer risk their career advancement if they stop operations due to a WHS concern?
Providing Safety Procedures That Are Easy to Use
Our role in the process is to provide you with resources. These not only make safety more efficient and effective but are also easy to use, cost-effective to implement and prove themselves as a profit-oriented investment.
From a big-picture perspective, we provide:
- Work Health and Safety Management Systems,
- Work Health and Safety Management Plans,
- SWMSs for both principal contractors and their contractors, and
- More specific Industry Packs which bring together the system and SWMS resources most suited to 23 separate trade/industry specialisations.
We can also tailor a solution to your specific needs.
If you have needs concerning subcontractors, the following four resources are available:
- Subcontractor Management Policy
- Subcontractor Safety Checklist
- Subcontractor Register
- Subcontractor or Visitor Attendance Register
Together these usually cost $81, but as a promotion for this article, we've created the Subcontractor Management Pack. It includes all four of these items for just $50 (a 37% discount). You can locate the individual items by following their links or view the group pack discount by clicking here.
Think Safety, Create Culture and Resource Safety Well
At Occupational Safety Solutions, we help you help your people so they can help your bottom line. We encourage you to:
- Adopt a 'perspective' rather than an 'attitude' mentality.
- Stay committed to safe work procedures because of the lives affected.
- Build a work culture that is aware of the many people involved, is well-led, cuts no corners and empowers people to speak up.
- Put easy to use and cost-effective resources in your people's hands.
We help you with the first three, and we resource you with the fourth. We can equip and support you, and we're here to help. Perhaps you need an entire WHS Management System or Management Plan, individual SWMS, a specific Industry Pack, or maybe our Subcontractor Management Pack special for just $50.
Whatever safe work procedures you need, we're here for you.
Phone 1800 304 336 and you will almost always have an immediate connection with an expert. If you'd prefer, we can call you; simply request a callback here. We look forward to helping you keep your people safe while also building your profit!